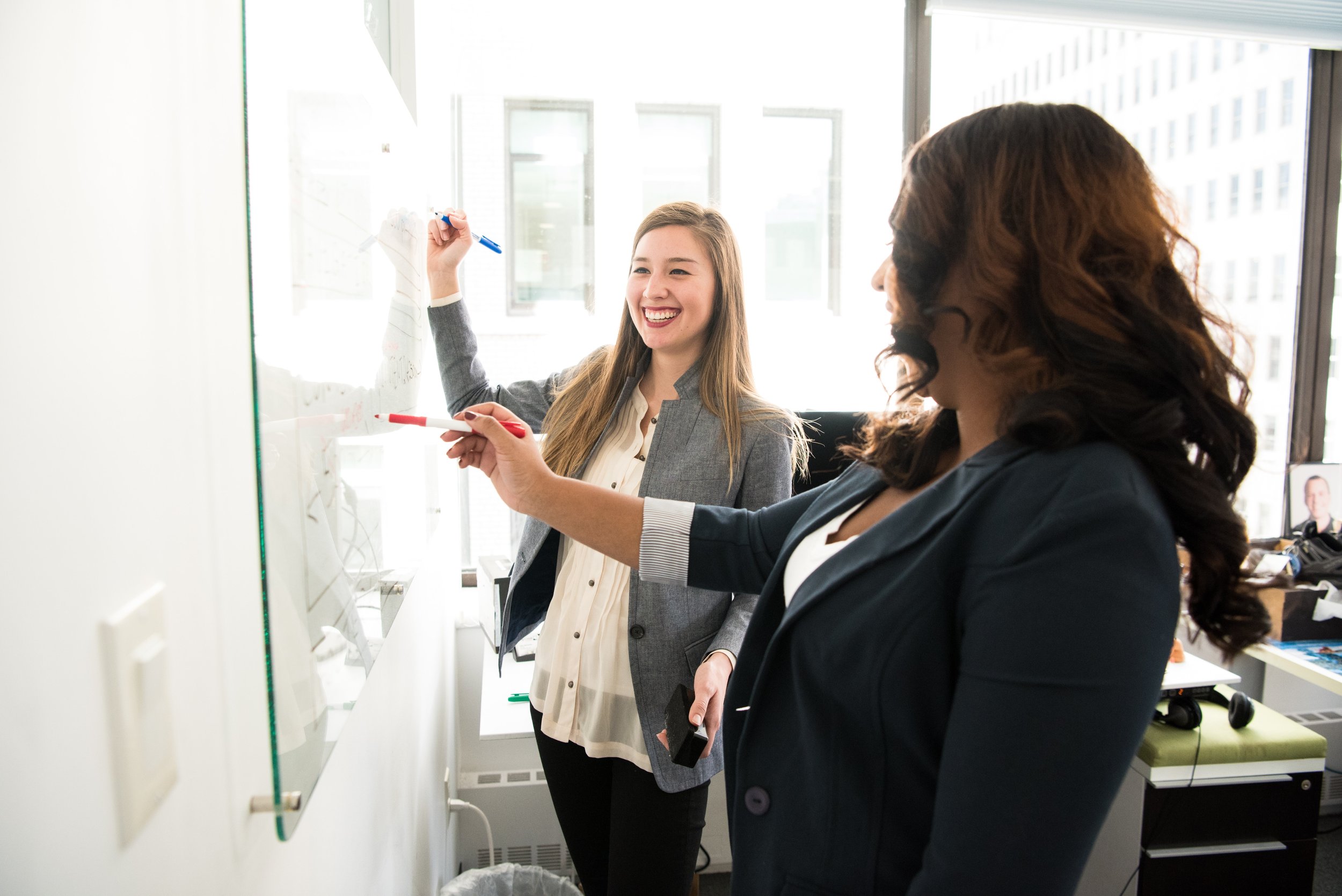
TWI / Training Within Industry
Transforming efficiency
In today’s fast-paced and competitive world, businesses are constantly searching for ways to improve efficiency, productivity, and employee satisfaction. TWI offers a proven methodology to achieve these goals and more, revolutionizing the way organizations operate and making it a game-changer for businesses across industries.
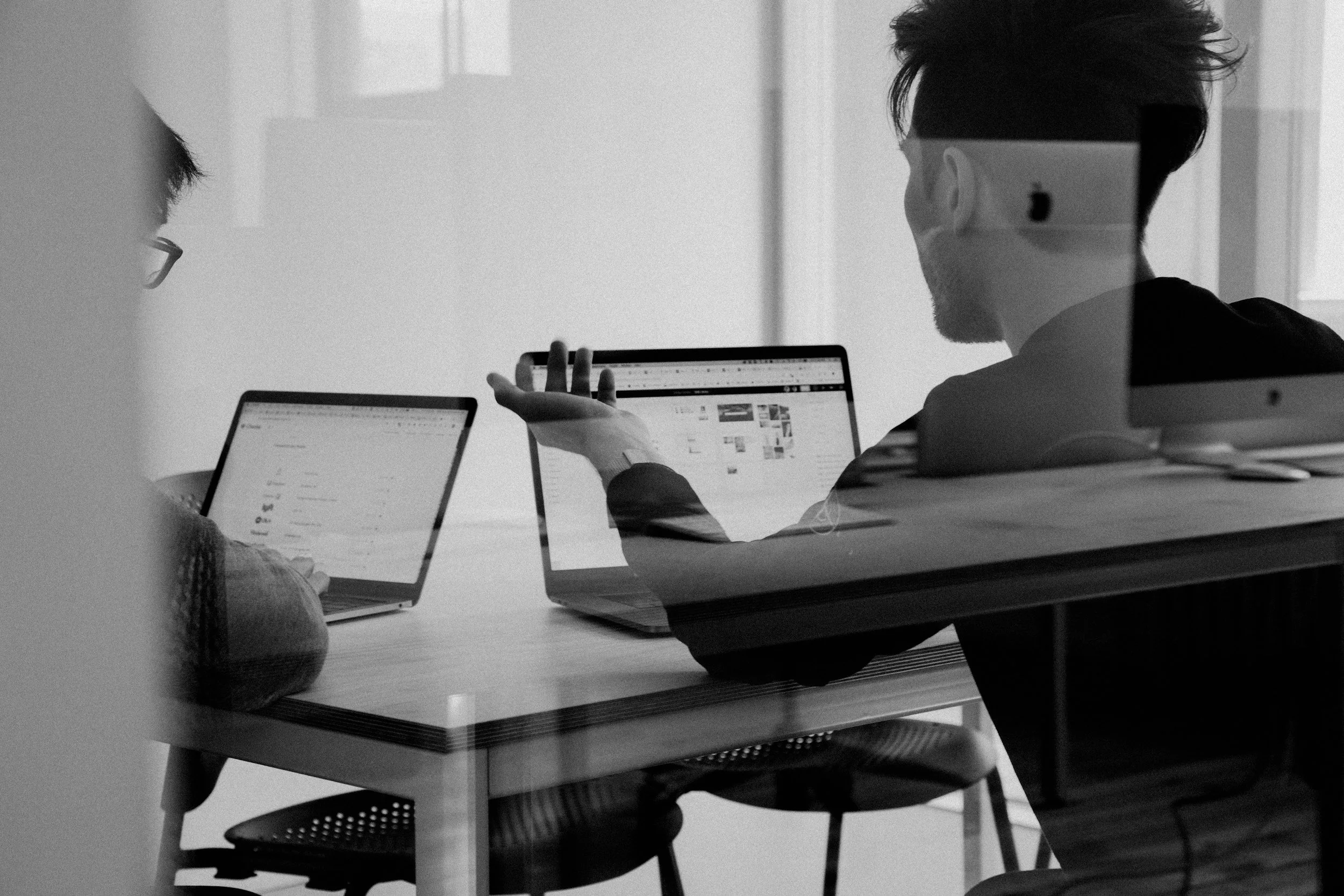
-
Job Safety
Workplace accidents can harm workers, families, the employer and its entire workforce, as well as damage facilities and equipment, increase scrap and downtime, and much more. Job Safety Training (JS) is an accident-preventing methodology based on a simple and logical framework centered on analysis of potential accident causes and possible countermeasures.
The central model of the JS program is the accident chain. Causes and events leading up to an accident are interlocked like the links of a chain, or an "accident chain" and the supervisor’s job is to break the chain. Through both classroom exercises and examples brought in by your staff, the accident chain model is used to "map out" the problems on the board for analysis and application of the Job Safety "Four Step Method." Indirect and direct causes of personal injury and/or property damages are examined in order to create countermeasures that are enforceable and measured for success.
The combination of classroom training and on-site implementation enhances knowledge retention through a "learn-by-doing" methodology. Key to the Job Safety program is a workplace inspection, during which all participants visit the worksites of two trainees. These two participants lead the group through their areas to apply the Job Safety methodology to their work, not only inspecting equipment and machines, but observing employees’ capabilities, mental and physical state, work attitude, use of protective gear, handling of tools, etc.
Lastly, Job Safety emphasizes the vital role of leadership and the different types of supervisory styles. Supervisors are taught to examine the possibility that the supervisor himself or herself might be the very cause of a possible accident.
-
Job Instruction
Training Within Industry's Job Instructions (JI) course aims to reduce the inconsistency of work provided by your employees, thus resulting in waste reduction and efficiency improvement. Often called the missing link to Lean, JI focuses on reducing the variability in our people.
Developing a flexible, effective workforce requires standardized practices. Job Instruction (JI) teaches supervisors how to quickly train employees to do a job correctly, safely, and conscientiously. Participants learn how to effectively break down a job and deliver instruction for individual tasks-- training one-on-one, hands-on, and one step at time. This standardized training method fosters the conditions needed for process stability.
The program uses real world examples to demonstrate the poor ways in which problems are often handled in the workplace, and offers a standardized alternative to drive positive results. The first two sessions center on learning the "Four Step Method," a simple, straight forward, and easy to implement process focused on Preparation, Presentation, Application, and Testing. The remaining course time is given to participant instruction demonstrations from your workplace to practice the Four Step Method. Unlike any other training, the TWI "learn by doing" methodology requires participants to immediately implement their new knowledge in the workplace.
Job Instructions is especially effective when combined with TWI’s Job Relations (JR) program, which focuses on building positive employee relations using the same TWI Four Step Method.
-
Job Relations
Supervisors and team leaders are in a pivotal position to both implement and sustain change. However, they're often promoted from the shop floor in recognition of their knowledge about product, processes, and materials. Many do not have the supervisor skills to effectively instruct employees, gain loyalty and cooperation, and solve problems. Training Within Industry's Job Relations (JR) course provides a countermeasure to help supervisors address employee morale and problems that arise when implementing a strategy of continuous improvement.
In this course, managers and supervisors learn how to apply standard work to managing employees in order to build positive relationships and a strong team. By communicating how each employee is doing, giving credit when due, telling employees in advance about changes that will affect them, and making best use of each person’s ability, your management team can set a positive productive environment for the entire workforce. Developing and maintaining these good relationships prevents problems from arising and is paramount to earning loyalty and cooperation from others.
When problems do arise, Job Relations uses the "Four Step Method", a proven method of getting the facts, weighing options and deciding, taking action, and checking results. The course emphasizes that people must be treated as individuals to provide a foundation for good relationships. Benefits experienced from practicing Job Relations include increased productivity, improved attendance, better morale, and higher employee retention rates.
As more and more companies embrace Lean techniques, it has become increasingly obvious that company culture remains to be the biggest challenge. TWI Job Relations is the solution.
-
Job Methods
Job Methods Training (JM) teaches supervisors how to improve the way jobs are accomplished. The aim of the program is to help produce greater quantities of quality products in less time by making the best use of the manpower, machines, and materials now available.
Job Methods, just as in Job Instructions and Job Relations, teaches the "Four Step Method:" a simple, straight forward, and easy to implement process focused on Preparation, Presentation, Application, and Testing. Job Methods teaches supervisors how to break down a specified job exactly as it is currently completed, question every detail, develop a new and improved method, and then apply the new method.
By applying six simple questions -- why? what? where? when? who? how? – to every step of the production process, supervisors gain understanding of the core value of each detail. Through eliminating, combining, rearranging, and simplifying these details, an improved method is created. Lastly, participants are given the tools to communicate the value of the new process, acquiring employee commitment of the new method.
Job Methods yields significant benefits including reduced cost through productivity gains, increased throughput, and reduced work in process.
-
Advanced Job Relations
Advanced Job Relations is a tool for supervisors that covers how to do one-on-one coaching to address current performance and professional growth.
By following the 4 Step Process, we begin to not only grow our current leaders, but we are better equipped to assess and mentor all of our subordinates to be ready to take the next step in their professional growth. This is done so by learning the skill in counseling by repetition and practice until it becomes natural.
It is best suited for our second line leaders and above but can also add huge value if there is ability to trust first line leaders with this responsibility. A firm grasp of JR is required due to their close working ties. Students will learn how to communicate in a productive two-way conversation taking in the employees meaning not just the words they use.
-
TWI Problem Solving
Job Relations teaches us:
“A problem is anything, as supervisors, we have to take action on.”
Yet, how often are we putting in our efforts to solve a problem only to have the same problem pop up again and again. One of the struggles we face is finding the time to dig to the root cause of each issue. TWI Problem Solving(PS) teaches individuals to work together using the entirety of the TWI program to quickly find the root cause. In any problem we face, the root cause usually comes from one of three areas:
- Insufficient training
- Lack of consistent leadership
- Process issuesThis in where PS takes the participants through a 15-hour journey on how to use Job Instruction, Job Relations and Job Methods to quickly reach the source of the problem.
Job Instruction, Job Relations and Job Methods are a prerequisite for TWI Problem solving.

Leverage the full potential of your workforce, driving sustainable growth and success while creating a culture of continous improvement.